Plunger Pump: A type of reciprocating pump that utilizes a solid body to change the volume of the pumping cavity.
Plunger pumps are perhaps the most common reciprocating pumps used in the industry. They are able to pump fluids at a steady flow rate regardless of the pressure at the outlet of the pump.
For more information on how a reciprocating pump works, its components, types, and terminology, see Reciprocating Pump.
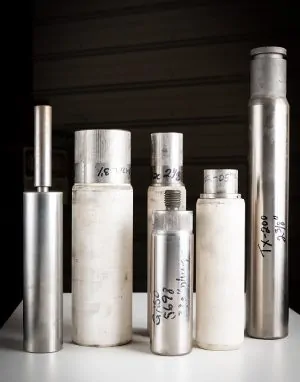
Plunger Pump Plungers
Plungers for plunger pumps are available in many sizes and materials. Depending on the application, plungers may be machined in-house or purchased from suppliers. Generally, plunger pumps are made to accommodate several different diameters of plungers to increase flow or increase pressure. The stroke length is set by the power end of the plunger pump and is more difficult to alter.
Plungers are commonly made from a ceramic, carbon steel, or stainless steel base material. They are then left as is, or coated depending on the application they will be used for. Several common types of plunger coatings are listed below.
Ceramic: Plungers are often fully ceramic, or have a ceramic coating around a base material. Usually alumina, the ceramic is resistant to abrasives and high mineral content.
Tungsten Carbide: A coating is applied to a base material to help harden the surface, reduce wear from wear. Tungsten Carbide plungers are not specifically corrosion resistant and are recommended for uses where wear on the plunger is more of a concern.
Rokide: Also called Chrome Oxide, a rokide plunger is often used in pumping fluids with little lubrication, such as amine and glycol. The rokide is a hardening and protective coating to a base material.
Hard-Co: The plungers base material is coated for additional protection against wear and corrosion. This coating consists of a nickel-chrome alloy which is non-porous. It is the standard plunger used for non-ceramic applications.