Reciprocating Pump: A positive displacement pump which utilizes a plunger or piston to change a cavity’s volume, and produce a pressure differential.
A plunger pump operates using the reciprocating motion of plungers or pistons. Depending on the design of the pump, the use of a single or multiple plungers may be used.
How a Reciprocating Pump Works
To help visualize how a reciprocating pump works, let’s look at a single piston and split the process into four parts.
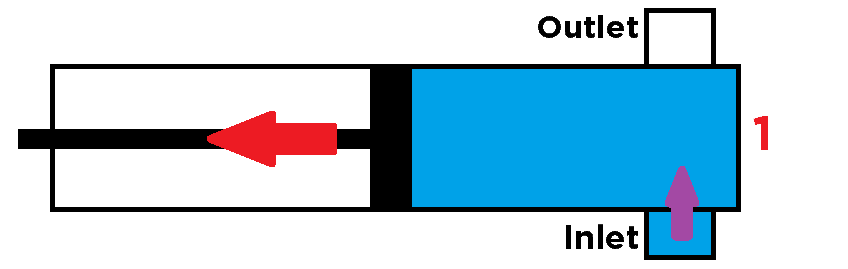
Action 1: The plunger or piston is pulled back. The action increases the volume of the cavity. As the cavity volume expands, fluid is drawn in through the inlet to fill the expanding cavity.
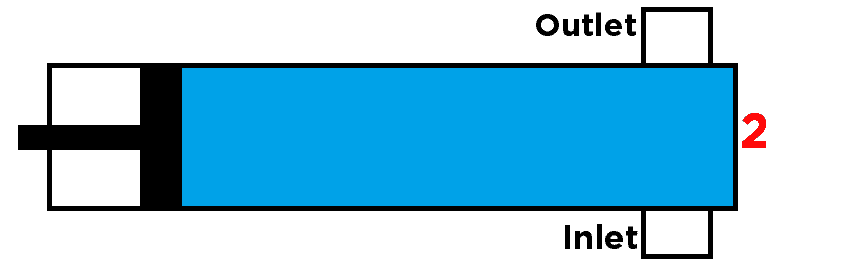
Action 2: The piston has reached it’s maximum displacement. Since it is not moving into or out of the cavity, fluid is not flowing through the inlet or the outlet.
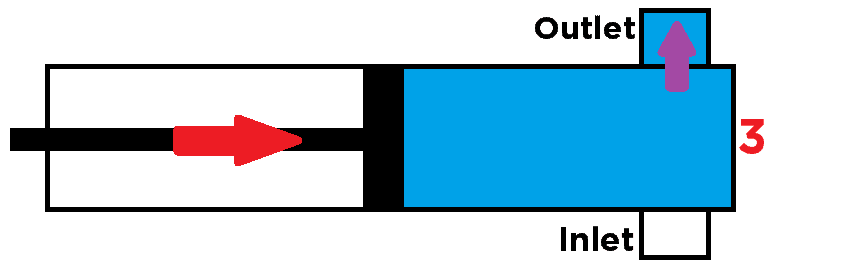
Action 3: After reaching it’s maximum position, it is then pushed back into the cavity. During this process, the piston applies enough pressure to the fluid to overcome the pressure in the outlet of the pump. This pressure differential pushes the fluid from inside the cavity through the outlet of the pump.
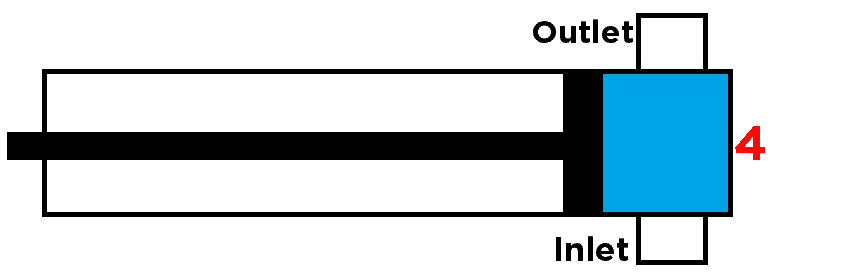
Action 4: The piston reaches its maximum extension into the cavity. Here the volume of the cavity is at a minimum and fluid is not flowing through the inlet or the outlet. The next action repeats the process, starting again with action 1.
The process of how a reciprocating pump works can be seen here in action from start to finish:
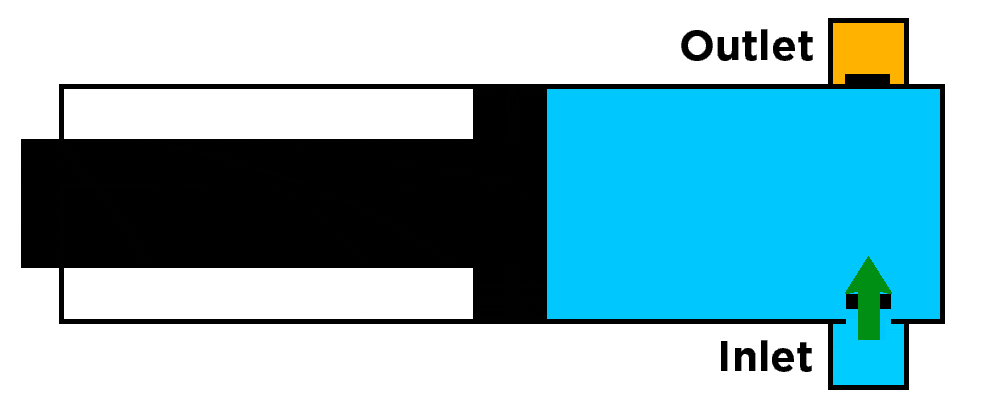
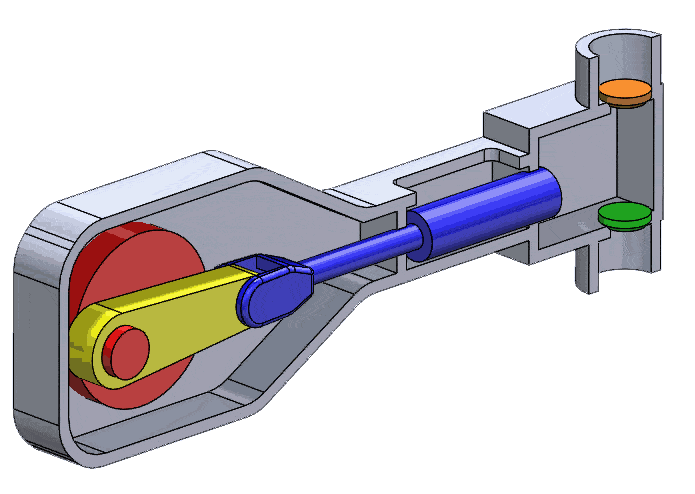
View our reciprocating pumps for sale
The key components used in reciprocating pumps are
- Piston, Plunger or a diaphragm: All these parts have the basic functionality of moving the liquid inside the cylinder. The piston is a lubricated sliding shaft that moves inside the cylinder and pushes the liquid in a forward and backward motion, creating a cavity and a high volume pressure at the outlet. In a diaphragm pump, the diaphragm is used to avoid leaking of the liquid since it completely seals the liquid to penetrate outside, and hence they are especially useful when the liquids are dangerous or toxic. In a plunger pump, there is a high-pressure seal that is stationary and a smooth cylindrical plunger slides through the seal.
- Crank and Connecting rod: Crank is a circular disk attached to the motor and used to transfer the rotary motion of the motor to the piston. Piston, in turn, moves in a reciprocating motion with help of a connecting rod.
- Suction pipe: Liquid flows from this pipe into the cylinder. One side of the pipe is immersed in the liquid and the other end is connected to the cylinder.
- Delivery pipe: This can be understood as an outlet pipe. One end is connected to the cylinder while the other is towards the discharge/Outlet.
- Suction and Delivery valve: It adjusts the rate of the flow of liquid at the suction and discharge points.
Reciprocating pumps are different from Centrifugal pumps on basis of its working, features, applications etc. The main difference is that Impellers are used in Centrifugal pumps whereas in reciprocating pumps piston is used to move the liquid. Centrifugal pumps continuously discharge the liquid, unlike reciprocating pumps. They are used for high viscous fluid and are lighter in weight, less expensive as compared to reciprocating pumps.
The basic Quality standards of reciprocating pumps include ISO13710, API (American Petroleum Institute) standard 674, API standard 675 “Positive Displacement Pumps- Reciprocating” and Reciprocating Pump Standards, Hydraulic Institute.
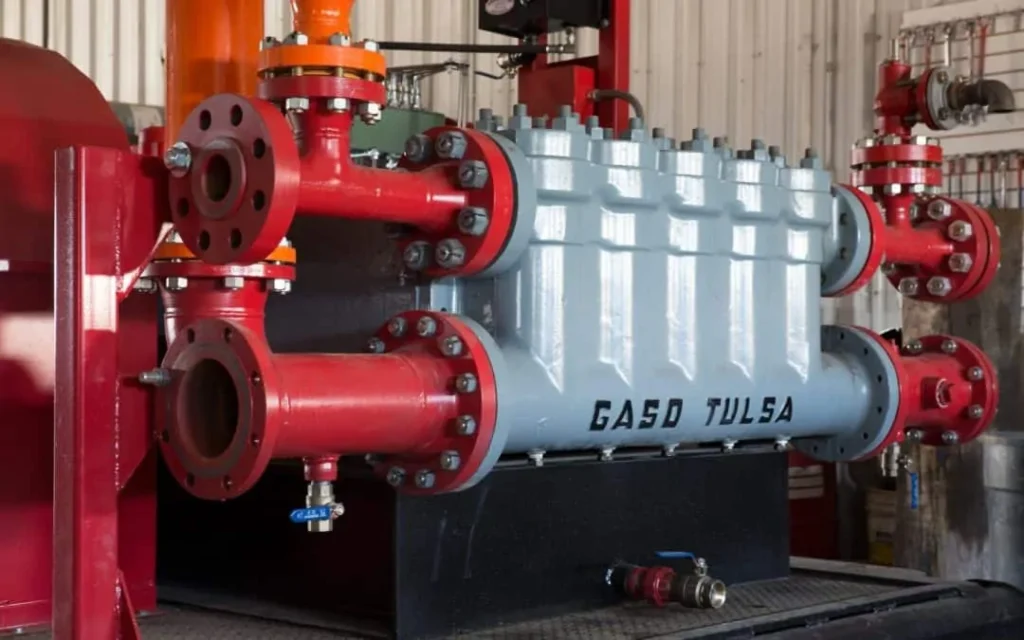
Advantages of Reciprocating Pumps
- High Pressure, Low Flow Applications: Reciprocating pumps are generally designed to pump in low flow, high head applications. One of the most extreme of these applications is water jet cutting, where only a few gallons pass through the pump per minute but exceed pressures of 10,000 PSI.
- Proven, Common Technology: Reciprocating pumps are one of the oldest, most proven pump types. Today, a wide variety of reciprocating pumps can be found in many different materials, types, and sizes. Reciprocating pumps range from less than 1 horsepower to over 3,000 horsepower.
- Durability: Reciprocating pumps are used in some of the most abrasive and corrosive applications. Fluid ends and fluid end parts can be made of many different materials such as stainless steel, aluminum bronze, tungsten carbide, ceramic, and more. A wide selection of valve types is used in abrasive applications such as pumping cement, sand slurry, mud, etc.
- Efficiency: Reciprocating pumps operate at high a higher efficiency compared to other pump designs. In most cases, at any setpoint, reciprocating pumps operate around 90%.
Factors that determine the efficiency of a Reciprocating Pump
There are several performance indicators of a reciprocating pump which determine how effectively it works. Following are some of the key performance indicators:
- Brake Horsepower (BHP): How much is the actual power requirement at the input shaft to achieve a desired pressure and flow.
- Capacity: It can be defined as the total volume of liquid/flow delivered per unit of time.
- Slips: Slip is the capacity loss as a fraction or percentage of the suction capacity.
- Mechanical efficiency: Working at full load pressure and speed is 90% to 95% depending on the size, speed, and construction.
- Pressure: Mainly, the suction and the discharge pressure in a pump.
- Displacement: Also known as GPM, it is the calculated capacity of the pump with no-slip losses.
Disadvantages of Reciprocating Pumps
- High Maintenance / Short Life: The main disadvantage of a reciprocating pump is high maintenance and short life. There are many parts in the pump works, all constantly changing directions. Unless careful maintenance takes place, the lifespan of the pump is greatly reduced. While pumps such as centrifugal pumps can last 15 to 20 years with little maintenance, a reciprocating pump requires higher levels of attention and rebuilding several times within the same time frame. The cost of a reciprocating pump rebuild is usually inexpensive which still makes them cost-competitive compared to longer-lasting, higher-priced pump designs.
- Pulsations: A characteristic of reciprocating pumps is the production of pressure pulsations through the pump inlet and outlets. The reciprocating motion of the pump produces these pulsations. Increasing the number of pump chambers can greatly reduce the pulsations produced, but it does not remove them completely. To negate damage to piping and surrounding systems or the pump itself, pulsation dampeners must be installed. Further system design can further decrease pulsations to nearly zero. In all cases, overall system design is important when using reciprocating pumps.
Reciprocating Pump Variations
Plunger pumps come in a variety of styles, shapes, and sizes. The specific type of pump chosen for an application takes into account the pressures encountered, the flow rates needed, measurement and control systems, fluid viscosity and corrosivity, pipe material, etc. Careful attention should be given to the application before selecting a pump. Selecting the wrong pump for a job can result in damage to equipment, piping, systems, and possibly endanger personnel.
Types of Reciprocating Pumps
The following are commonly known types of reciprocating pumps:
- Single-acting reciprocating pump: This has one suction valve and one discharge valve. When the piston is moved backward, suction happens and when it moves forward, the delivery valve opens up to discharge the liquid.
- Double-acting reciprocating pump: Unlike a single acting pump, here there are two suction and delivery valves. When the piston is moved forward or backward, with each stroke, both suction and expulsion happen simultaneously. Thus it requires two inflow pipes and two outflow pipes. Some of the common applications of these kinds of pumps are in Salt Water Disposal, Well Service, Descaling, Hydraulic Fracturing, and Oil & Gas Pipelines.
- Double-acting – Air and Steam pumps: These are double-acting pumps where steam, air, or gas is used to transmit power to the liquid through the piston. The ratio of total steam force (steam pressure per unit area x area of the steam piston) to total liquid force (pump head x area of the liquid piston) helps determine the efficiency with which the pump produces pressure. They can operate at any point of pressure and flow, within a flexible range. Because of these features, steam-driven pumps are mostly used in the refineries for pump-out service, with low NPSH and the fluids used are hydrocarbons mostly with high viscosity and high temperature. National, Gardner Denver, Oilwell, Gaso, and Wheatley are known as key manufacturers of such pumps.
- Simplex, Duplex, Triplex, Quintuplex Pumps: Many reciprocating type pumps are simplex(one), duplex (two), or triplex (three) cylinder. Duplex pumps are usually used where the two pumps can be used alternatively. Such pumps are commonly used in oil-line pumping, mine de-watering, and chemical and petroleum products transfer, but has many more applications. A triplex pump consists of three plungers, with the aim of reducing the pulsation of a single reciprocating pump. Quintuplex pumps are designed with a gear case that assists in a high-pressure task. Common applications of which are in cement slurries, sand-laden fluids, crude oil, acids, mud, and other oil well-servicing fluids. Well known manufacturers for these types of pumps are National, Gardner Denver, FMC, SPM, Oilwell, Kerr, Union, Gaso, Emsco, Aplex, and Wheatley.
- Metering Pumps: A metering pump is usually used where the rate of flow of the liquid needs to be adjusted in a specific time period. Most of the metering pumps are piston-driven and are called Piston pumps. Piston pumps can pump at a constant flow rate against any kind of discharge pressure. Both Piston pumps and Plunger pumps are reciprocating positive displacement pumps that use a plunger or piston to move fluid/substance through a cylindrical chamber. Manufacturers such as Lewa, Watson Marlow, and Bredel offer metering pumps at competitive prices.
Reciprocating Pumps can also be classified according to the number of cylinders: Single cylinder and double cylinder pump. They are also sometimes classified according to their operation, known as simple hand-operated reciprocating pump & power-operated deep well reciprocating pump.
Common Application of Reciprocating Pumps
Reciprocating positive displacement pumps are highly effective, where a high degree of accuracy and reliability under different ranges of conditions that are required. Reciprocating pumps with very high efficiency are often available in a wide range of hydraulic, mechanical, and material options. They are widely used across industries such as chemical, petrochemical, refinery, pharmaceutical, cosmetic and water treatment. Typically, these types of pumps are used for applications such as Salt Water Disposal, Well Services, Descaling, Hydraulic Fracturing, and Oil & Gas Pipelines. All types of reciprocating pumps are easily available in the market to meet the diverse demands, as per different processes and applications. Piston pumps are widely used in applications such as Energy Recovery, Steam Recovery and hazardous area pumping and are available with manufacturers such as Union, Gardner Denver, Worthington, and Wilson Snyder.
Diaphragm Pumps are commonly used for Sludge Transfer, Acid Pumping, and Chemical Fluid Transfer and are easily available with manufacturers such as Wilden, Sandpiper, ARO, Roughneck, and Graco.
All the mentioned manufacturers in this article, offering various kinds of pumps hold a good reputation with respect to quality, price, revenue (value), and market share and are preferred by many consumers. However, a thorough check of all its features, specific to your process application, should be ideally done to buy the most suitable reciprocating pump, which can be used for a longer period of time requiring low maintenance, ease of operation, and easy availability of its spare parts.
For further queries or assistance, please feel free to contact us.
Reciprocating Pump Terms
Reciprocating pump terms are based on how the fluid is pumped (action) and the number of plungers or pistons (arrangement). For example, a Union TX-200 is a “single-acting triplex plunger pump”, a Gaso 1849 is a “double-acting duplex plunger pump”, and an Oilwell B-558 is a “single-acting quintuplex plunger pump”.
Reciprocating pumps have thee types of “actions”. Single, Dual, and Direct Action:
Reciprocating Pumps have a few different types of arrangements. You can learn more about each one below:
Reciprocating Pumps can use several different methods to change the volume of the cavity to produce flow. The most common are:
Piston / Swab
(More Info Coming Soon)
Diaphram
(More Info Coming Soon)
Power Zone Will Help Select and Supply the Right Pumps for Your Application
Contact us today to get started!